On April 25, 2023, Johns Manville Engineered Products restarted a glass melter, after it was taken out of service for a routine rebuild. The furnace had previously reached the end of its service life after a record campaign of 10 years.
“This is an outstanding achievement from a technology perspective,” said John Vasuta, President of Johns Manville Engineered Products. "The teams from Trnava and our Johns Manville Technical Center in the U.S. worked together extremely well and did a fantastic job to achieve such a long life for the furnace. The rebuild also went remarkably smoothly."
This furnace rebuild also affirms Johns Manville’s commitment to continue serving the industry in Europe with regional production.
At JEC World in April 2023, Johns Manville showcased its full potential of StarRov® single-end rovings, MultiStar® multi-end rovings and ThermoFlow® and StarStran® chopped strands – all of which expand the capabilities of thermoplastic and thermoset composites. In addition, Johns Manville showcased its innovative Neomera® PA-6 organosheet products, which feature exceptionally good mechanical properties thanks to their patented reactive sizing technology.
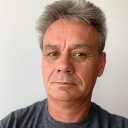
4 Questions for Miroslav Bučány,
Project Engineering Manager in Trnava, Slovakia
The commissioning of a new glass furnace is a major technical achievement and requires a lot of experience and technical expertise. As the project manager, Miroslav Bučány was heavily involved, so we asked him some questions about the rebuild.
1. How did the teams from Trnava and Johns Manville Technical Center work together to achieve such a long life for the old furnace?
Due to our long company history, Johns Manville has already mastered multiple furnace rebuilds. Of course, each rebuild teaches you something new, and the technological components are also constantly improving. Nevertheless, the project can only be brought to success if the teams work together effectively. The technological capabilities at the JMTC combined with the experience of our employees in Trnava, who work at the furnace every day, were fundamental factors in the record-breaking lifespan of the old furnace.
2. What difficulties did the team in Trnava face while performing the rebuild of the furnace?
The project and operations team faced a few technical and time-related challenges. We had to replace the existing abatement/filter technology entirely, as well as innovate with basement scrap vibrating conveyors. Implementing automation in the winding area was also a big hurdle. All this required extra effort and engineering worked hard to coordinate all external vendors, JM operations and maintenance teams to keep the project within the approved cost and time constraints.
3. What technical advancements facilitated the successful rebuild of the furnace?
The successful rebuild of the furnace was enabled by advancements in technology, including implementation of improved melter design layouts, several small improvements in the forming area, a new abatement/filter technology system, new technology for collecting waste fiber in the basement, innovations in the combustion system, more accurate temperature gauges and sensors, and enhanced materials. These technical advancements will ensure smooth operation of the furnace, improved efficiency, reduced emissions, and an extended lifespan.
4. What impact has this furnace rebuild had for the European market?
This successful rebuild has proven Johns Manville's commitment to serving the European industry with regional production. It’s a reaffirmation to our customers that we will provide them with a security of supply from Europe. We are especially proud to serve the market with products made in Trnava.
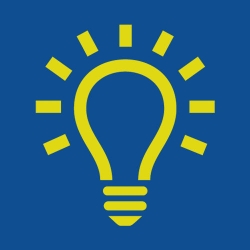
Did you know...
...900 tons of refractory material and 150 tons of construction steel were built into our new furnace
...60,000 hours of work was carried out to complete the rebuild
...2 days after the furnace generated its first glass, we were able to produce our first sellable material
...1,500°C / 2,730°F is the temperature inside the furnace
-
Engineered Products
-
Engineered Products
-
Engineered Products
-
Engineered Products
-
Engineered ProductsIndustry Insights, Sustainable Innovations, and Market Adaptability: A Comprehensive Overview from the Global Gypsum & Insulation Conference 2023
-
CommunityInternational Glass Artist Blends Illusion and Reality Using Johns Manville Materials
-
Engineered ProductsJM Reinforces Global Manufacturing Footprint as Tom Kendrick Returns as Global Fiberglass Commercial Director
-
Engineered Products