When it comes to high-temperature operations, insulation specifications can vary greatly, and in an effort to save money, it can be tempting to disregard safe-to-touch recommendations. ASTM C1055 (Standard Guide for Heated System Surface Conditions that Produce Contact Burn Injuries) recommends that pipe surface temperatures remain at or below 140°F. The reason for this is that the average person can touch a 140°F surface for up to five seconds without sustaining irreversible burn damage.
ASTM C1055 determined that five seconds is the most probable contact time in an industrial setting. In high ambient temperature environments or where there is an elevated risk to the worker, many process engineers will use 120°F as the maximum safe-to-touch temperature to further reduce the risk to workers.
The chart below breaks down how skin reacts when exposed to surfaces at varying temperatures. Note that as temperatures rise, burned skin tissue can actually become white. This is indicative of irreversible burn damage and is so severe that the pain can be replaced by a feeling of numbness.
Some safety organizations have taken proactive measures to incorporate safe-to-touch temperature standards that reference ASTM C1055. In June of 2010, California’s OSHSB amended their General Industry Safety Orders (Section 3308) to read that, “pipes or other exposed surfaces having an external surface temperature of 140°F (60°C) or higher,” should be insulated or otherwise guarded against contact. OSHA regulation 1910.261(k)(11) states, “all exposed steam and hot-water pipes within 7 feet of the floor or working platform, or within 15 inches measured horizontally from stairways, ramps, or fixed ladders, shall be covered with an insulating material or guarded in such a manner as to prevent contact.”
Over the last decade, innovative products and materials have greatly impacted the industrial insulation industry. Industrial Insulation Group, a Johns Manville Company, and other manufacturers have successfully introduced new insulation technologies that are thinner than traditional insulations; however, these thinner products typically require multiple layers to achieve the same thermal efficiency as traditional insulations. This can drive up both material and labor costs. As a result, these types of insulations are typically only used in highly specialized applications where saving space is an absolute necessity and temperatures are relatively low.
Consider the following scenario comparing the performance capabilities of calcium silicate and silica aerogel. Calcium silicate must be three inches thick to meet safe-to-touch standards. To achieve this thickness, you can either use two layers of 1.5-inch-thick insulation (which allows you to overlap the joints), or you can use a single layer of 3-inch-thick insulation. In contrast, silica aerogel requires four layers of insulation to achieve comparable performance. Notably, three extra layers of insulation will cause a substantial increase in the cost of both material and labor.
3″ Calcium Silicate
Surface Temp = 138.2
Pipe O.D. = 6″
Operating Temp = 600ºF
Ambient Temp 75ºF
Wind Speed = 0 mph
Emissivity = 0.04 (Aluminum)
1-2 Layers Required
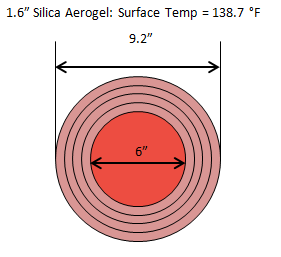
1.6″ Silica Aerogel
Surface Temp + 138.7ºF
Pipe O.D. = 6″
Operating Temp = 600ºF
Ambient Temp = 75ºF
Wind Speed = 0 mph
Emissivity = 0.04 (Aluminum)
4 layers required
When specifying the amount of insulation needed to achieve safe surface temperatures, several design parameters must be identified. Surface temperature is determined by a combination of wind speed, ambient and process temperatures, and the use and type of jacketing. Readily available software can help you easily identify how much insulation will be necessary for you to achieve specific surface temperatures.
Regardless of the material type selected, we encourage engineers to perform independent quantitative analysis to determine the appropriate insulation thickness based on the design requirements for the project. One reliable and unbiased software program for performing such calculations with many variable inputs is 3EPlus and is available as a free download at www.pipeinsulation.org.
In order to achieve maximum personnel protection, Industrial Insulation Group recommends adhering to the ASTM C1055 standard and offers a spectrum of traditional insulations that balance process control, low surface temperatures, and cost to fit the unique needs of the industry.
- See more at: http://www.iig-llc.com/blog/2015/02/too-hot-to-handle/#sthash.FyQW1PRw.dpuf