Mineral wool pipe insulation has been used successfully in many industrial applications due to its dimensional stability at high temperatures, thermal performance, low weight and economical installed costs. Mineral wool pipe insulation is made from basalt, a volcanic rock, and bound with a thermosetting resin. Given these features, there are additional factors to weigh when considering the use of this product.
There are two major components of mineral wool insulation: basalt fiber (≈98%) and thermosetting resin (up to 5%). Mineral wool pipe insulation products have a density of approximately 8.0 lbs/ft3, which provides sufficient compressive strength for reliable performance in areas that don’t see foot-traffic.
Although the basalt fibers can withstand temperatures in excess of 2000°F, the binder that holds the fibers together begins to oxidize (or burn off) at approximately 450°F. When this happens, the basalt fibers remain intact, but they are no longer bonded to each other, reducing the insulation’s compressive strength. If the insulation is not subjected to a compressive force, the material typically retains its loft and performance, even after the binder has burned off. However, once the binder is gone, any portion of the insulation that was exposed to temperatures in excess of 450°F will experience diminished compressive strength.
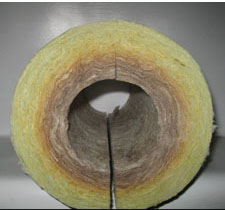
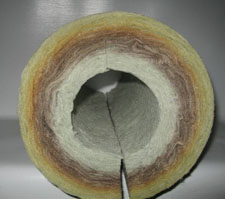
While the reduction in compressive strength alone won’t impact the thermal performance of the insulation, any area that has been exposed to temperatures greater than 450°F is at an increased risk for impact damage. When mineral wool is exposed to impact without the binder, it can compress the insulation. Naturally, this reduces the thickness of the insulation and its thermal performance, which can cause hot spots.
For this reason, applications need to be carefully considered to ensure that mineral wool will not be used in areas with high foot-traffic or the potential for loads or forces to be applied to the product. Should the application require higher compressive strength with more resistance to impacts and bumps, mineral wool is not the ideal solution. That said, mineral wool can be used in tandem with different products such as calcium silicate to capitalize on the economical performance of mineral wool as well as the benefits of other insulations to create a hybrid application. As with any product, there is no such thing as a bad material, only a material that has been misapplied.
For additional details on compressive strength, we encourage you to read the Technical Bulletin: TB011 Compressive Strength of High-Temperature Thermal Insulation.
Doug Fast is the Technical Service Specialist for the Industrial Insulation Group and responds to technical inquiries regarding mineral wool, MPT, calcium silicate and perlite insulations. His 15 years of experience in the building materials industry include the roles of building insulation technical specialist, product testing lab manager (acoustics, thermal and fire) and product development engineer for commercial roofing. He is a Licensed Professional Engineer in the state of Colorado and a LEED Accredited Professional.