Acting as hidden champions, they surround us every day to protect us and improve our lives: fiberglass mats. These engineered fabrics have a wide range of advantageous product characteristics and are, therefore, used in a variety of applications.

However, the manufacturing process is complex, and it is challenging to produce this nonwoven material at a high-quality level. In this article, we will explain how fiberglass mats are made and describe the individual production steps. But let’s start with a fundamental question:
What is a Fiberglass Mat?
A fiberglass mat (also called glass veil or glass nonwoven) is a flat fabric composed of chopped fiberglass oriented in a random pattern and bonded together. Originally
invented to replace cardboard in waterproofing membranes, fiberglass mats have long since become predominantly used in additional markets such as commercial and residential construction, energy storage and automotive. Fiberglass mats can be tailormade to fit the properties the end applications require by adjusting, for instance, the fiberglass (glass type, fiber sizing, fiber length, fiber diameter, fiber mixture), the binder systems, the mat thickness, and the mat density. Fiberglass mat is sold in rolls of various widths and lengths.
Process Overview
The production process we describe here is a wet-laid process, much like paper, but with some key differences that help us deliver products with superior performance. Let’s have a look at the individual manufacturing steps.
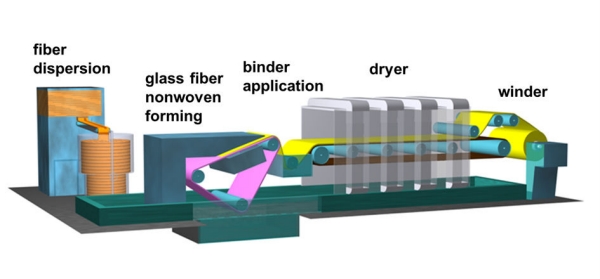
Fiber Dispersion

Glass fibers are available in a variety of lengths and diameters, which can have a big influence on the performance of fiberglass nonwovens. At Johns Manville, we produce our own fiberglass.

The glass fibers are added to a pulping system to break the bundles apart and suspend them. This creates a homogenous mixture. Whitewater chemistry is critical to keep fibers in suspension. Adding various processing aids to the water keeps the fibers separated in the process water. Without these, fibers would tend to bundle back together and form clumps in the process. The chemistry of the process water is very complex and controlling the process water is an important step in making quality glass nonwovens.
Mat Forming
Fiberglass mats are primarily produced on machines, which are typically 1.5 to 6.0 meters wide, with a closed loop process water system. The fiber stock gets introduced at the pulping step and enters the formation section where the fibers get distributed uniformly across the width of the machine.
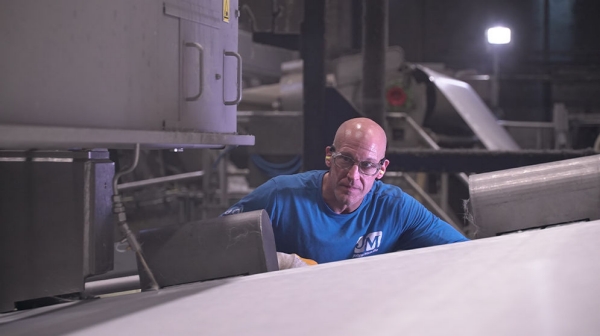
Through adjustments of the settings in the formation step, the final mat properties are influenced to deliver the performance needed for the finished product.
Tensile Ratio
When talking about sheet properties, you typically talk about properties in the Machine Direction (MD) or the Cross Machine Direction (CMD). The machine direction is the “long” dimension of the product and the cross-machine direction is perpendicular to that (the roll width). The following graphic shows some examples of how the fiber orientation can appear in a finished sheet.

The glass mat manufacturer must set a separate fiber orientation for each end use so that the necessary properties, such as optical surface quality or strength, are achieved.
Binding
Now that a formed sheet with the desired fiber orientation has been formed, the strength of the sheet is still relatively low. To achieve the ultimate strength and performance, a binder must be applied.

Early fiberglass nonwoven mats used urea formaldehyde binders, but through years of development, a variety of acrylics, including formaldehyde-free and bio-based, have been developed (learn more about Alpha Binder, JM’s formaldehyde-free, bio-based binder option). These binders add functionality and performance to the product. The flexibility of the Johns Manville process is such that one day we can make a glass nonwoven that feels as soft as cloth, and the next day we can make a strong, stiff glass nonwoven that can be used for a composite laminate process.
After the binder has been applied, the process moves on to the drying step.
Drying
To deliver a finished product, it is important to remove the water and activate / cure the binder. After the binder application, a continuous conveyor belt carries the material through the dryer where both of those steps get accomplished. Knowing the proper drying conditions is very important.
Finishing and Winding
Once the glass mat is dried, it moves onto the final steps of the process. The dried product is measured to maintain a uniform weight of the product. Additional sensors are available for binder content, thickness, and air permeability, and additional control loops can be developed to control those parameters by adjusting machine settings on the wet end of the process.

The full sheet is also inspected using an on-line web inspection system. These systems are very powerful with high resolution cameras that can detect major defects in the sheet before they make it to the customer. This data is provided in real time to the machine operators so they can correct the root cause of the defect even faster.

The final step before winding and packaging is the slitting step. Here the roll is cut to width and the formed edges are trimmed. This provides a clean, square edge on the finished product.

Once the material is slit, it is wound onto a mandrel, packaged, and sent off to the customer.
Process Wrap Up
With this information, you now have a comprehensive overview of the wet-laid fiberglass mat production process. Fiberglass mat lines are built with flexibility in mind, and here at Johns Manville we are able to adapt the process to produce the best possible materials for our customers. This adds complexity but delivers better products for our clients.
Visit our Nonwovens pages to discover our product offerings for a variety of applications and reach out to us to learn more about our tailor-made solutions for your business.
Contact us for detailed product information and support
-
Engineered ProductsWhy Exterior Sheathing Needs a Tough Partner – And Why Our Fiberglass Nonwovens Are Up for the Job
-
Engineered Products
-
Engineered Products
-
Engineered Products
-
Engineered Products
-
Engineered ProductsHow to Solve Industrial Filtration Challenges with Evalith® Micro Fiberglass Filter Tube Media
-
Engineered Products