In the south of Germany’s state of Thuringia lies Steinach, a small town surrounded by beautiful nature. Here is where about 85 Johns Manville employees produce high-quality fiberglass mat for roofing and composite materials. Their drive for innovation goes hand in hand with a passion for sustainable solutions. So, it’s not surprising that they installed a cutting-edge quality control system working behind the scenes to ensure that only the best quality materials reach our customers while contributing to a greener future.
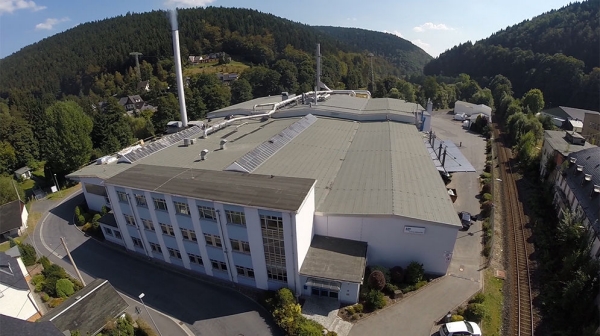
What is a Fiberglass Mat?
Steinach is one of two JM plants in Germany running fiberglass mat lines. A fiberglass mat (also called glass veil or glass nonwoven) is a flat fabric composed of chopped fiberglass oriented in a random pattern and bonded together. Originally invented to replace cardboard in waterproofing membranes, fiberglass mats have long since become predominantly used in additional markets such as commercial and residential construction, energy storage and automotive. Fiberglass mats can be tailormade to fit the properties the end applications require by adjusting, for instance, the fiberglass (glass type, fiber sizing, fiber length, fiber diameter, fiber mixture), the binder systems, the mat thickness, and the mat density. Fiberglass mat is sold in rolls of various widths and lengths.
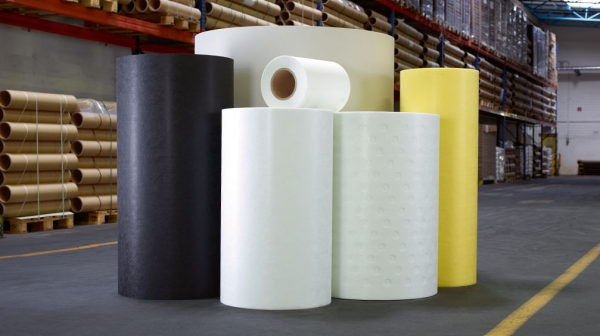
Detecting Flaws, Preserving Quality
Before a fiberglass mat leaves our production line every square meter gets monitored by a quality control system gauging area weight, thickness, and binder content. The full sheet is also inspected using an on-line web inspection system. These tools are very powerful with high resolution cameras that can detect major defects in the sheet before they make it to the customer. This data is provided in real time to the machine operators so they can correct the root cause of the defect even faster.
But what happens with material that has already been produced showing quality defects or needs to undergo further inspections?
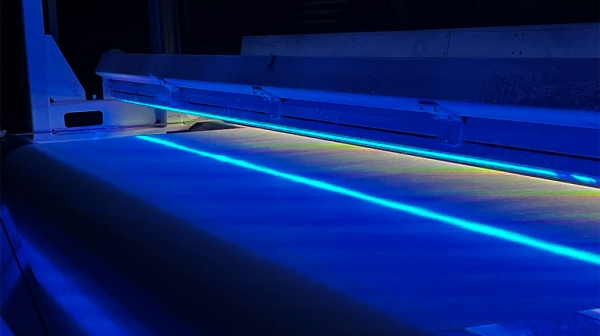
Sustainable Achievements Through Technological Progress
After the meticulous quality control process, the fiberglass mats that require further inspection are handled by a state-of-the-art winder machine. This unit unwinds the glass mat roll to the exact section that needs to be reviewed. If necessary, the part of the material with quality defects can be cut out and the roll can be taped back together again. This process enables a remarkable 90% of materials that undergo a second check on the converter machine to be sent to our customers as a product meeting all quality specifications. This also plays a crucial role in our sustainability efforts. It significantly minimizes waste and reduces the environmental impact associated with discarding flawed products.
Other JM sites use similar technologies but what sets the Steinach plant apart is its capability to produce and rewind jumbo rolls with a diameter of up to 230 cm / 90" on a 12" core. This ability allows us to meet the diverse needs of our customers.
"This process enables a remarkable 90% of materials that undergo a second check on the converter machine to be sent to our customers as a product meeting all quality specifications."
In a Nutshell
The combination of cutting-edge technology, stringent quality control measures, and a focus on sustainability at our Steinach plant allows us to deliver not only high-quality fiberglass mats but also to minimize our environmental footprint. Through this integrated approach, we not only meet the demands of our customers but also contribute to a more sustainable and eco-friendly future in the process.
-
Engineered ProductsWhat Keeps Energy Flowing: The Unsung Role of Materials in Lead-Acid Battery Performance
-
Engineered ProductsWhy Exterior Sheathing Needs a Tough Partner – And Why Our Fiberglass Nonwovens Are Up for the Job
-
Engineered Products
-
Engineered Products
-
Engineered Products
-
Engineered Products
-
Engineered ProductsHow to Solve Industrial Filtration Challenges with Evalith® Micro Fiberglass Filter Tube Media