Listen in on our next podcast episode as we get the latest update from our Plant Manager, Josh Canada, on our new polyiso plant in Hillsboro, Texas. This is our biggest plant yet and has state of the art technology to be a blue print for a brighter, more sustainable future at Johns Manville commercial roofing. This plant also has over 100,000 sf of warehouse space that will be used for staging and shipping our products to customers in this region.
Above It All is a podcast by Johns Manville dedicated to the roofing industry. The goal of this podcast is to bring knowledge from a Johns Manville perspective on trends, innovations, and people shaping the roofing industry. Join us as we dive head first into enriching conversations about the people and passion that are an integral part of the JM experience.
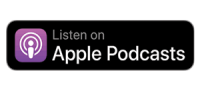
Transcript
Daniel Robbins: So here we are for another episode of Above It All, a roofing podcast dedicated to the industry by Johns Manville. Today is very special. I have with me Josh Canada and he is our new plant manager for our Hillsboro plant in Texas. Josh, how you doing, sir?
Josh Canada: Doing very well, thank you.
Daniel Robbins: So Josh, this is a big deal because apparently, our Hillsboro plant is state of the art compared to our other plants and going forward probably when we make new plants, it’s gonna be a really nice blueprint. But before we get into that stuff, I kinda wanted to get your story a little bit. What is your background? What brought you... I guess what is your experience that brought you here to the plant manager position at JM?
Josh Canada: Yeah, so prior to working for JM, I worked in the tire industry for Bridgestone Firestone for about 20 years. Moved around quite a bit with my family, lived in Iowa, Indiana, and Texas. Texas is my home. So once we ended up back in Texas, I really wasn’t looking to leave... Sorry about that.
Daniel Robbins: No worries. You’re a busy guy these days, I know.
Josh Canada: But no, I got back to Texas, me and my wife made the choice to not make another move with Bridgestone, so I actually was a HR director for a healthcare company in Abilene for a couple of years.
Daniel Robbins: Oh wow.
Josh Canada: My passion’s always been in manufacturing and I was constantly looking for a good opportunity to get back into manufacturing, and the Hillsboro project came up on my radar. It was a greenfield project, new plant, all the way from beginning to end. I was excited about it, so next thing you know, I’m applying and interviewing. And that’s kinda how I ended up at JM.
Daniel Robbins: So did you start with an education knowing that you wanted to do something similar to this or is your education background completely different?
Josh Canada: Yeah, so my education is in business, which is kind of a generic degree. Kinda wish at this point in my career that I’d spent some time in engineering, would have been helpful but the business education has served me well, a lot of leadership classes and things that have helped me.
Daniel Robbins: I have the business background too and, of course, we work with a bunch of engineers here at Johns Manville, and I must say that the business background helped me be able to communicate much better on a project basis with everybody, all walks of life, right? Engineer to the salesperson, and I think that’s really cool. I can’t imagine how that’s helping you in your role, but let’s move on to the plant. This is a state-of-the-art plant. I know there is some really special elements, things that you can point out about what makes this plant different and state of the art. Let’s talk about some of those things.
Josh Canada: Yeah, so like you said, state of the art equipment, the plant from its layout design, the construction is all planned so that it could be what we desired at the other location. So a cross-functional team a couple of years ago, started looking at this project and really put together all the good elements from the other locations, left out the bad, modified and what we have today is really what you would want for a state of the art polyiso facility.
Daniel Robbins: Yeah, and I think that word bad is intense. I think probably it was just what they were at the time, the codes and everything have changed completely, right? So now we’ve built something that’s exceeding the code probably. So let’s talk about some of those environmental elements ‘cause I know you were talking to me about how the plant is able to recycle a certain way. Can you touch on that a little bit?
Josh Canada: Yeah, so our goal is to be zero landfill. We started out with that in mind when I interviewed our environmental EH&S person, and that’s one of the things that I discussed with them. It’s not easy to start out with, to go to a zero landfill but you really have to look for those outlets to get rid of your waste. Our process, just like every other process, does produce waste, but there are places that we can dispose of that so that it goes into another use, but no, as far as our line goes, it is designed to be as efficient as it can be. We have a thermal oxidizer that burns off any fumes that come off of the production line, and then we have a dust collector that collects any dust and puts that into a form so that it can be disposed of.Daniel Robbins: Now that burning of the fumes, I’ve never seen that before at a plant, that’s new. Do you know what happens when we don’t burn the fumes, what kind of environment we create?
Josh Canada: Yeah, so there are certain chemicals during the reaction process that give off fumes that can be bad for the environment, so we actually went above and beyond in this case, to add the thermal oxidizer. Quite a few plants don’t have that, just exhaust to the atmosphere, and it is allowed by the EPA within limits, but in our case, they went above and beyond and added the thermal oxidizer so that we don’t put off anything, so...
Daniel Robbins: That’s incredible. So that thermal oxidizer, is it a small machine or... When I was there, I noticed there was a massive ventilation system. Is that a part of what you’re talking about?
Josh Canada: Yes, yeah, it’s very large. It sits outside the plant on the west side and it’s probably the size of two rail cars...
Daniel Robbins: Oh my gosh.
Josh Canada: It’s an expensive add-on to the plant.
Daniel Robbins: But what a cool thing to be able to kinda set that standard. I think people across the world who are doing business in the manufacturing industry probably would appreciate less emissions and however we get there, I think, is a big deal.
Josh Canada: Yeah, and our safety and our environmental goals, we wanna be the top in the industry. So on the safety side, you’ve got OSHA STARR VPP is... That’s something that we’re pursuing. We have to be in operation for three years before we can apply for that. And then again, the zero landfill, but both of those goals are not easily achieved, but we’re committed to our teammates and our community that we’re gonna... To be a good corporate citizen.
Daniel Robbins: Very cool. So moving on, we have our environmental piece, that sounds like it’s state of the art, the manufacturing capacity. This is one of the biggest polyiso plants we’ve ever made. What does that look like to you, from the warehouse to being able to crank out X amount of materials?
Josh Canada: Yeah, so our line, because of the speed and the size of our laminator, it will produce 30-40% more than the other locations, so the other five iso plants. So that, in itself, is quite an achievement. So the warehouse as well, it was designed so that we could have high volume products going out the door. We can load as many as five trucks at a time in the warehouse, and we can process 60-70 truck loads a day, outgoing material.
Daniel Robbins: Wow. Now, with those materials, yes we are getting polyiso, of course, in our inventory, we’re creating it there at the plant. But then are we also keeping everything that our contractors are using in that region as well, such as TPO, accessories, things like that?
Josh Canada: Absolutely, yep. We have the whole JM roofing system here ready to ship with the iso boards.
Daniel Robbins: That is awesome. So when I was there, I saw the warehouse, which was absolutely stunning, and someone pointed out, too, that there was a cool feature on the warehouse where there always needs to be a fire-barriered room. Did I say that right?
Josh Canada: Yes.
Daniel Robbins: And the one that’s in the... This place is the biggest, I think JM has. And it was interesting because I had no idea that you need to separate products a certain way. Can you tell us, and for our listeners, a little bit about that process?
Josh Canada: Yeah, so anything that’s hazardous, flammable, like you said, would go into that room in the warehouse. It’s got fireproof walls, doors. It also has a system that, in the case there were a fire, it would flood the room with foam and it would extinguish the flame, so it’s very safe.
Daniel Robbins: Is the foam thing a new apparatus or has it always been, we flood the room with foam?
Josh Canada: It may be new to JM, I don’t think it’s a new apparatus.
Daniel Robbins: It is very cool, though. Alright, so we’ve talked about the amazing amount of truck... Oh yeah, one thing that I did notice too, is our rail capacity. What is the actual... I think in other polyiso plants I’ve been to, you can get one rail car back there. How many rail cars can we get at this plant?
Josh Canada: Yeah, so we have... Being close to the... Where most of the raw materials are coming from, we have an advantage that we can leverage for the company in the event that there’s a shortage or if there’s a hurricane down on the coast, things like that. We can store as many as 18 rail cars on our spur. We also have our own rail car mover where the other locations are at the mercy of the rail yard that’s local to come move their... Spot their cars for them, so we can actually move our rail cars around ourselves. The store can fit 18.
Daniel Robbins: That’s huge. What’s that piece of machinery called?
Josh Canada: We call it a rail car mover.
Daniel Robbins: Oh, it’s just a rail car... [laughter] Nothing tricky, nothing fancy.
Josh Canada: Pretty simple. [laughter]
Daniel Robbins: That’s cool, though. It looked like a massive piece of machinery, and so really that’s gonna help too... Is that gonna expedite the manufacturing process as well? Is it just gonna add to that ability to get quick turnover on product?
Josh Canada: Yeah, so it really helps us to... Gives us an advantage whenever it comes to not being at the mercy of the local rail yard to spot the cars. It could be middle of the night, we run out of product, where we’re getting close, we can go grab a car and move it up ourselves.
Daniel Robbins: Now, historically, do you feel like it can take days sometimes for that... Their... The company rail car mover to come through?
Josh Canada: They typically only service certain days of the week. So, in our instance, we get service on Monday, Wednesday and Friday. The other plants, it just depends on the schedule for the local rail yard.
Daniel Robbins: Gotcha, so there is a little bit of flex with potentially being able to accommodate our manufacturing needs, but the fact that we’ve got this means that now we get to call the shots with how fast things go, which is huge. Let’s move on. I... JM is about people, JM is about passion, performance, and protection. So what are some of the things you believe in, as a plant manager, that you wanna bring to this relationship with your employees, like principles, qualities, things like that?
Josh Canada: Yeah, sure. So my goal as a leader has always been to help people achieve their goals. I always wanna treat people the way I wanna be treated. One recent example that we were able to do with the teammates here is giving them a say in how their shift configuration looks. So we presented them with multiple options and we let them actually vote on what their shift configuration would be, so the hours, and the change over times, and that kind of stuff. So they really appreciated that, but we also have committees that we’re forming, so that employees on every shift have a say in different things. We have an Employee Involvement Committee. People can help decide how we do recognition, company dinners, things like that. And then also, a Safety Committee, so that they have a strong say if there’s something that needs to be addressed on the floor in regards to safety.
Josh Canada: From a career standpoint, we offer pay-for-skill for all positions, we offer cross-training between departments, and then if the folks that wanna pursue higher education, we offer tuition reimbursement. So our goal is to make the Hillsboro plant a place that people wanna grow their career and stay long term. We’ve got a $65 million asset sitting here and it’s absolutely worthless without people, so we are well aware of that, and we know that the most important ingredient to this whole thing are the people.
Daniel Robbins: Very cool. So when can we expect... Are we... We’re already shipping... We started shipping a few months ago, right? From the warehouse. When did we get our first board off the line?
Josh Canada: So we are starting our provisional acceptance of the line the second week of March. And we should be going to 24/7 late March, early April, we’ll be producing boards.
Daniel Robbins: Very cool. Well, I know a lot of customers will be super excited because what a crazy industry it is in that southern region for roofing in general, I think.Josh Canada: Yep.
Daniel Robbins: But yeah, we’re out of time. Josh, thank you so much for being on the podcast.
Josh Canada: Alright, thank you.
Daniel Robbins: Thanks everyone for tuning in. Go subscribe if you haven’t yet, Apple Podcast. But yeah, go there, download the app if you don’t have it. It’s just the easiest way to get the latest episodes and you’ll get notifications on your phone, and that way you don’t miss a beat when it comes to product launches, new initiatives that we’re doing as a brand, and then also just general knowledge about what we do, the services that we offer, the products that we offer, and how those impact our customers in a positive way. With that, stay safe everyone and we will catch you next time.