Above It All podcast episode #27 features Bituminous Product Manager, Jacob Heaps, for Johns Manville Commercial Roofing. Join us as we discuss the latest advancements in SBS self adhered technology, and a fairly new SBS self-adhered base sheet Dynagrip® Base SD/SA. We are dedicated to providing product excellence for our customers as well as value when installing materials, we think our SBS self-adhered line can do just that, get the scoop in this episode.
Above It All is a podcast by Johns Manville dedicated to the roofing industry. The goal of this podcast is to bring knowledge from a Johns Manville perspective on trends, innovations, and people shaping the roofing industry. Join us as we dive head first into enriching conversations about the people and passion that are an integral part of the JM experience.
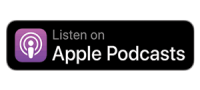
Transcript
Daniel Robbins: Check, check, check one, two. Alright, I’m gonna start. We are back for another episode of Above It All, a roofing podcast, dedicated to the industry by Johns Manville. So I’m here with Jacob Heaps today. We have had this product out for a little bit, it’s called DynaGrip SD/SA, and so Jacob is gonna enlighten us a little bit on this product, and then some of our other self-adhered offerings that we do have that would go great with it and would just be a great product in general to use. So with that, Jacob, how are you doing, sir? Thanks for being on the podcast.
Jacob Heaps: Hey, Daniel, I’m doing well. Hope you’re doing well as well. Thanks for having me.
Daniel Robbins: Yes, of course. And are you excited about the DynaGrip SD/SA? I know there hasn’t been a ton of self-adhered offerings in the past for SBS.
Jacob Heaps: Yeah, definitely, I think at JM, we really pride ourselves on offering, especially in the SBS realm, a highly customizable system. We have like that products for every type of need, every type of building out there. And I think DynaGrip SD/SA and our DynaGrip self-adhering product line in general, really fits that mold, definitely something we’ve been working on for a long time. Like you said, we’ve had it on the market for a while, it’s always been there but we didn’t pay too much attention to it. But the last couple of years, we’ve done a lot of development work with it, really revamped the formulation, gave us higher tack, gave us a higher softening point so you don’t see the same sort of softening in the field that you used to see with our old formulation.
Daniel Robbins: I love that. That’s our experience as a manufacturer over 160 years, I feel like just coming to perfection is when you do get to create a perfect product and it may not be exactly the right thing at first, but eventually because this company has the infrastructure, we get it right. So that’s amazing. So with that, let’s talk a little bit about this product, the SD/SA, and how it brings value to customers.
Jacob Heaps: Yes, like I mentioned, we have a ton of base sheets out there when it comes to the standard ways of putting down an SBS membrane; you got hot asphalt, you got torching or cold adhesive and DynaGrip SD/SA is really our self-adhering workhorse base sheet. The SD/SA actually stands for sand in SA, that really indicates to the customer that one side of the sheet’s gonna have your release liner and a tacky adhesive, it’s gonna go down to the deck or the surface substrate, and then the SD is the top portion, a standard portion. The cool thing about that is it allows you to quickly get down a self-adhesive base and then you can put either hot asphalt, or a cold adhesive, or a torch plier cap above that.
Daniel Robbins: Is there one type of application that works better over that? Or they all just work the same and the sand is there just to really help even take in more of whatever membrane goes on top?
Jacob Heaps: Yeah, we have a couple of systems that we like to tout, I guess. Like a “stick one torch one” are the pretty common system we see on the field. That’s really the biggest that using the DynaGrip as the base and then coming over the top with a torch, a DynaWell type product. And the cool thing about that is that the heat, the heat from the torch actually really helps bite the DynaGrip down into the substrate. So you already get a fairly good bond with the SD/SA, but I think one of the inherent disadvantages of self-adhering technology is that you’re really at the mercy of the substrate sometimes and the installer. So if you have any sort of dust or dirt or anything that could impact that adhesion, that could negatively impact your overall system. But coming over with a torch on top, you get that extra heat that really helps melt that DynaGrip into the substrate, and then you get a nice asphalt-asphalt bond with the cap sheet once you finish your torching. I think you know but at the end of the day, what we’re trying to do is offer the customer and our clients whatever sort of option they wanna go with, so if you do wanna put a hot asphalt down or if you do wanna go with a cold adhesive you have that option as well with the sandy top.
Daniel Robbins: So we just did a training recently for some of our pinnacle contractors, and we did stick one torch one and then we did also just full self-adhered, I believe it was a DynaGrip self-adhered over the SD/SA. And I noticed that when you torch... I haven’t had my hands on a ton of self-adhered membranes, but I noticed with the new manufactured ones that we’ve created, when you torch, it gets to this fine kind of gumminess. With the SA products, I noticed they already have that gumminess to it so they’re ready to be adhered, but then also sink into that membrane, which to me is, it’s super cool ‘cause I feel like you’re doing far less work and you’re getting the same benefits out of that membrane.
Jacob Heaps: Yeah, I think the cool thing about it is, so I’d mentioned the SD/SA. We also have, to your point, we did a training with our SA/SA membrane and that just again, indicates that the product has two side itself adhered, so SA/SA would have a release liner on the bottom, which you would remove and stick down to the substrate, and then you’d remove the release liner on the top, and you could actually put a self-adhering cap or another ply of DynaGrip, if you would like, on top of that. And yeah, I think the big benefit of that is, as you put that down on the roof and get a few thermal cycles going, a couple of days of sun on that, you really get a true thick asphalt-asphalt bond, which is a nice benefit of ours. I think there’s a couple competitors out there that use a film-type surface for all their SA/SA products, and so you’re inherently gonna have a disadvantage of having a non-native material in between your asphalt at that point, and so the ability to go asphalt-asphalt really allows the adhesive to really wet together and really get a nice, nice, strong bond and just continues, like I said, that continues to get stronger the more thermal cycling and heat exposure it goes through.
Daniel Robbins: That’s very cool. So you mentioned the release liner, I know that that’s been a touchy thing in the past because everyone’s been trying to figure out the best way to set up their release liners. For us, how have we... You mentioned a little bit, I know that it’s like a two-part release liner in all of our self-adhered products. Correct?
Jacob Heaps: Correct. So yeah, we have a split back release liner on the bottom portion of all our products and not a lot that really just lends itself to easy install for the installers, right? You can fold back and butterfly half of the sheet at a time, which allows you to minimize the number of people that need to be there helping with the install. It also helps stop any sort of accidental sticking that you have where you might develop a fish mouth, or something like that, where you get some of the product sticking to the substrate where you don’t want it to, and you get wrinkles in sheet and stuff, so yeah, I think that the two that split back offers a benefit in the installation.
Jacob Heaps: And then on the SA/SA sheet we have a full width release liner on the top. The cool thing there is, like I mentioned, some of the competition has permanent film stuck on there and you can walk on those, which is definitely a benefit to the installer, but you can do the same thing with ours. The only difference is that when it comes time to really put the system together, you’re taking that film out of the system and you’re just getting straight asphalt to asphalt. So like I said, the top film on the SA/SA definitely offers benefit as well of walkability as well as... But you still end up with that asphalt bond at the end of the day.
Daniel Robbins: That is very cool. And to that point about the walkability, I notice, yes, like with the self-adhered products, they have that extra kind of elasticity to them that will get more benefit from being out in the sun. But I noticed too, when you walk on it, it’s not gonna get damaged like if you heat it up, your top membrane with a torch and then walked over it. I didn’t notice the same type of tracking, that’s for sure.
Jacob Heaps: Yeah, and that’s always one of the inherent disadvantages, I think, of self-adhered, historically, is that you kinda have to balance that adhesion aspect of it with your high temp stability, and so I know that was one of the big things that we looked at whenever we were re-formulating was how can we optimize that relationship. And it really goes into the science behind the asphaltic formulation, I think that’s really where JM excels, innovation and looking at the science behind what goes into the membrane, how to make the membrane last, how do you make the membrane easier to use. I think our DynaGrip product line is really a good example of that in the last few years.
Daniel Robbins: That is very cool. So with the future of self-adhered technology, are we seeing... The better we make products, are we seeing more people leaning towards that, or do you think it’s kind of still a healthy mix, people like torching, but people also like the speed and labor benefits of the self-adhered?
Jacob Heaps: No, I think self-adhered in general is on an upward trend, right? The other three installation methods kinda naturally have some drawbacks. So hot asphalt you have, it’s super labor-intensive, there’s not a lot of installers out there who are doing it anymore, every day there’s less and less kettles out there, it’s smelly, so that’s a major drawback for hot. Then cold adhesives you have generally, they’re solvent-based right, so you have high VOCs in some. They take about a month to cure sometimes, so again, drawbacks there. And then torching is... We’re seeing a lot more restrictions on who can install, you have to have approved installers and stuff, so that’s definitely limiting this as well.
Jacob Heaps: And self-adhered I think is really, really a cool technology because it’s really taking advantage of the natural adhesiveness or the natural tackiness of the asphalt. Asphalt in itself is a great adhesive. You look at 90% of the roads or something out there are asphalt-based roads, and all that’s really doing is they’re using asphalt to stick a bunch of rock and stuff together. So great natural adhesive, and I think the rise in SA products across the industry is really just showing that people are starting to take advantage of that, you don’t have to add a secondary adhesive to it, you can build it right into the compound.Jacob Heaps: And then yeah, I think from a labor standpoint, in general right, labor’s becoming stricter or it’s harder and harder to find labor out there and self-adhering is really... I don’t wanna say foolproof, but out of all the three installation methods it’s really the easiest, probably, to teach someone. You can get someone throwing down a couple plies pretty quickly with minimal training.
Daniel Robbins: Have we done measurements on these SBS/SA systems, like how much more work and productivity, or I guess how much more productivity a crew can get out of this versus asphalt or torching?
Jacob Heaps: We haven’t, no. I think that will come down to... I think there are some crews out there who can put down hot asphalt pretty quickly, so I think we have to specially pick who we compare against on some of those. But I think in general, to your point, we did that training the other week and we see them... You can put down two plies and explain what you’re doing in less than 10 minutes.
Daniel Robbins: That sounds so fast.
Jacob Heaps: And so I think that’s a big benefit. Like I said, there’s not a whole lot of trickiness when it comes to the seal of the roof, right? You just have to make sure your end laps are put down correctly, the side laps are actually fully self-adhesive as well in all these products. So all the products have a removable release liner on the side laps, so as soon as you push those two together you get a nice bite and you’re basically, for all intents and purposes, waterproofed from the minute they’re stuck together.
Daniel Robbins: Very cool, and I know you mentioned for the adhesives that they do take that longer cure time, what’s the cure time like on the self-adhered?
Jacob Heaps: So you will get initial bite especially in a full SA/SA system. As soon as you touch those two together, they’re tough to adjust. So I think that’s something that as an installer you definitely wanna watch out for, which could be a drawback as well, I guess in the products. But if you line it up correctly, like I said, as soon as you stick them together you’ll have a nice bite. When you’re putting it down to a roof, a substrate, like I said you’ll get... The bond usually will enhance with thermal cycling. So within 24 hours though, you should have a bond that’s pretty close to full strength there. Definitely up there, comparable with cold adhesive adhesion after only 24 hours of being put down.
Daniel Robbins: Very cool, very cool. So, we are out of time. Where are some other places that they could get in touch if people wanna know more about this product?
Jacob Heaps: Yeah, if you go to jm.com and go into the brochures section, we have a little section about our DynaGrip product line as well. We also have another product line called CleanBond on the West Coast, more predominantly on the West Coast, another SA type product offering that we have as well. And then I think our JM Vapor Barrier SAR also utilizes this technology. So if you wanna check on any of those product data sheets as well on jm.com, it’d be a great resource for you.
Daniel Robbins: Very cool. Well, Jacob, thank you for your time and hopefully we can have you on again soon.
Jacob Heaps: Alright, thanks Daniel.
Daniel Robbins: Thank you. And that’s the podcast. Thank you all for joining us on this journey. For our listeners who have subscribed and for those new coming, please get tuned in. There’s lots of good information if you’re interested in commercial roofing, if you’re interested in JM, we hoped that we provided a suite of information so that you are not left out by any means. So go check the podcast out, Apple Podcast, or you can go to our website, JM.com and then go to commercial roofing. And then you’ll be able to pick our roofing blog. And with that you’ll be able to look at all the episodes we have. There’ll be some press releases, there’s also some... We got some of them translated or transcribed, sorry. Transcribed so you can read the whole podcast as well on some of those episodes. But yeah, that’s it. We’ll catch you next time. Stay safe out there, bye.