Above It All podcast episode #26 features Manager for National Preferred Accounts, Mitch Bortner, and Research Manager, Francis Babineau, for Johns Manville Commercial Roofing. Join us as we discuss the impact the pandemic has had on growth of the cold storage sector. Learn more about what challenges need to be considered when designing your next cold storage project.
Visit our resource page on cold storage here.
Above It All is a podcast by Johns Manville dedicated to the roofing industry. The goal of this podcast is to bring knowledge from a Johns Manville perspective on trends, innovations, and people shaping the roofing industry. Join us as we dive head first into enriching conversations about the people and passion that are an integral part of the JM experience.
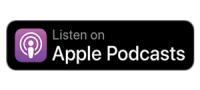
Transcript
Daniel Robbins: Here we are again for another episode of Above It All, a podcast dedicated to the roofing industry by Johns Manville. Today is really interesting because we’re covering a topic that I know we’ve covered a little bit in the past, maybe through some campaigning and some stuff we put up on our website. We really haven’t gone in deep and talked about what it means, and kind of what we have resource-wise dedicated to making sure that our customers can get it done right. So, with that, we’re going to talk about cold storage. So, we have JR Babineau and I have Mitch Bortner, and they’re going to discuss a little bit about what cold storage is and what it means for the customer from our point of view. How are you both doing today?
Mitch Bortner: Doing well, Daniel.
JR Babineau: Doing great, Daniel.
Daniel Robbins: Before we go into kind of some questions about this product and kind of its application, and well, it’s not really a product, but it’s really a technique and its application. What is cold storage? Let’s talk about what it is and where we run into it in the industry.
Mitch Bortner: Yeah, so cold storage, it’s very interesting, it’s a niche market, and it’s really grown in popularity recently because of COVID. It used to be that these buildings were built by an end-user, so think of Kroger. And there’s also a sector called PRW, publicly refrigerated warehouses, and they would also build. But here recently, because of COVID and the shift to online, there’s been a lot of speculative development in this sector. And it really didn’t attract it before because it was pretty... It’s expensive to build. A cold storage warehouse costs four times as much to build as a traditional, Amazon-type, just box warehouse. So pretty interesting and very specialized. And from a roofing standpoint, it’s really important that you get these systems right, because if you don’t, you’re going to have problems inside these buildings and with all the products that are in there, it’s just imperative that you get these system right. I think JR could speak more to what’s required for a tight envelope at one of these buildings.
Daniel Robbins: Yeah, JR, before we talk into the technical stuff, I guess, Mitch, is this something that you’ve been working on more than ever recently, really kind of tackling this market?
Mitch Bortner: Yeah, so a little background. I’ve been involved in this industry in one position or another for 15 years. I’ve been at Johns Manville for three years. I kind of brought my relationships and industry knowledge to Johns Manville. Saw this is an opportunity to pursue because these buildings are very specialized. There’re certain roofing contractors that are really good at this and some need a little more help. So that’s why we started this initiative to develop some details, put some knowledge around it, do things like these podcasts, just to help our contractors become successful at these projects, because they’re very attractive projects. There’s a lot of insulation on them, some of them are fully adhered, so great industry to be involved in.
Daniel Robbins: Well, thanks for giving a little backstory and context to that. Let’s talk more about the demand. Where is the demand for cold storage buildings headed? Is this something that has increased with more home delivery service?
Mitch Bortner: Yeah, as I mentioned, it’s really increased. We’re looking at, and this is pre-COVID, an additional hundred million square feet required in the US in the next five years, so it’s definitely growing. And it’s going to be more than that because of the shift to online grocery spending. And then there’s new companies being formed. There’s Cold Summit Development. There’s Agile Cold Storage. And there’s also Vertical Cold Storage that I just saw. And this is nice because there’s been massive consolidation in this industry recently. The two main players are Lineage and Americold, and they own 70% of the PRW market.
Daniel Robbins: Oh wow.
Mitch Bortner: It’s nice to see these new companies springing up with being funded by private equity to maybe a little more innovation and more competitors in the market.
Daniel Robbins: That’s very cool. I got a question for JR. JR, what are some of the main differences between installing a standard roof versus one over a cold storage facility?
JR Babineau: Sure. So really, the differences, Daniel, come down to just the challenges that are imposed upon the roof itself from a cold storage building. As Mitch had said, much more than a typical roof or a typical warehouse, the roof over a cold storage building has to deal with large temperature differences, right? We’re talking anywhere from just kind of refrigerated temperatures in the 30s or 40s, all the way down to well below zero, minus 20 or more. And those conditions are maintained 24/7, regardless of what the weather is outside. So big temperature differences across the roof, again, because of the big temperature differences, there’s a really big water vapor drive. A lot of moisture wants to try to get from the outside of that building inside, and then just much bigger concerns over air leakage and more of a need to control thermal bridging, thermal shorts. And all of these demands really mean that a cold storage roof is going to need more insulation. It’s going to need more attention to detail like roof-to-wall connections and penetrations. And as Mitch alluded to too, hopefully it will mean there’ll be... Have more adhered elements, though that’s not always the case. So just the demands on the roof really mean a lot more care is needed to do it right.
Daniel Robbins: That’s fascinating. You mentioned that thermal bridging. Can you explain and then kind of where are the biggest concerns for that and loss of internal temperatures?
JR Babineau: Sure, yeah, no problem. Thermal bridging is kind of a technical term but it really just means any sort of connection within, let’s say the roof, that’s going to let heat travel through a path other than through the insulation, right? We want all the heat loss or heat gain through that roof to ideally go through the layers of insulation, which of course will slow that down tremendously. But things like structural connections are often some of the biggest concerns for thermal bridging, think any sort of structural steel that somehow makes that connection from the cold inside to whatever the outside is, penetrations for mechanical systems can be sources. And then also relevant, even fasteners, now granted those don’t play as big a role as you would imagine the big kind of structural connections would. But even mechanical fasteners, if we’ve got a mechanically fastened insulation or mechanically fastened membrane, those can also contribute to thermal bridging but less so. It’s really the big things that are big steel items or big concrete items, those are the ones that really have to... We really need to watch out for the most.
Daniel Robbins: We just created this cold storage page, it’s going to be where everyone can go to get in touch or get all the information they want related to this topic. Are we hosting details there as well?
Mitch Bortner: No, if you would like to have the details sent to you, there’s a contact form available, fill out the contact form and those will be emailed to you by myself.
Daniel Robbins: That’s very cool though. We got 10 details. We also just recently shot a video of one of the details, I believe it was a drip edge. Does that sound familiar?
JR Babineau: Yes.
Daniel Robbins: To you both? I’m not the engineer but it was a drip edge and it’s fascinating to me getting to see how sealed up everything is. Does take those extra materials that you’ve been talking about, which I think can bring value to a sturdy roof system that’s going to be great for the end user. But then also the contractor being able to have a bigger project, I think that’s great. And we’ve been able to create details to help foster that a little bit more. Where do we go next with this? Are you just continuing to try and reach out to contractors and let them know that we have these details or what’s your strategy, Mitch?
Mitch Bortner: I am the cold storage vertical market leader here at Johns Manville. I have a lot of resources, I work with roofing contractors, owners, end-users, design-build GCs, had a lot of questions about things like expansion joints, how do we deal with those in a freezer, which is very challenging. And also, if an owner needs a roofing contractor, we know who those people are that are specialized in cold storage that are going to do a fantastic job. That’s a resource that I can offer and just being somebody to bounce stuff off of. These details have been presented before they were made public to lots of people and the feedback, we got was 100% positive, everybody really liked the details, they’re great details. So excited to do that. This is just phase one and then we’re... Like Daniel mentioned, we did a video last week that showed the roof to wall connection which is where most of the problems occur in a cold storage building. First of many and we’re just going to build out that cold storage page and be involved in the industry more so than we have in the past.
Daniel Robbins: Well, that’s very exciting. We are out of time. JR, Mitch, thank you both for being on the podcast and for everyone who’s been listening. Be sure to check out the page, our cold storage page. We’ve been kind of souping up and redesigning the website, so we’ve got a brand-new cold storage page. We’re going to have the video up on there shortly with the drip edge training tutorial. And with that we’ll wrap it up. Thanks so much everyone and thank you both for being on the podcast.