Since it was first introduced to their industry in the late 1970s, roof professionals have come to recognize the advantages of EPDM single ply membrane for low-slope commercial roofs. The technical term for this highly durable and weather-resistant material is “Ethylene Propylene Diene Monomer.” However, it is typically known by its acronym–EPDM.
Johns Manville has manufactured roofing materials since 1858, and it began selling and marketing EPDM in 1982. The company opened its own manufacturing facility for EPDM in Milan, Ohio; where they use state-of-the-art roller die extrusion equipment. Milan is the newest wide-sheet facility in the world.
Calendering: a traditional manufacturing Technique
After extensive research, including the assessment of durability, weather resistance, longevity, UV resistance and many other factors, the roofing materials experts at Johns Manville determined that there was only one way to make their EPDM membrane. The manufacturing facility in Milan makes EPDM using extrusion technology instead of calendering.
The process of using a “calender” to flatten rubber into thin sheets has been around for more than a century. In this process, heat-softened rubber polymer is forced through two or more rollers to create a sheet, and the resulting roof membrane–the EPDM–is then rolled, cured, packaged and transported to project sites for installation. While this technique and the resulting membrane was acceptable for the construction industry for many years, over time, limitations inherent to the calendering process have become evident.
According to the online research site Appropedia, “To begin the process the polymer must go through blending and fluxing before it goes through the calender.
Blending is a process that creates the desired polymer and fluxing heats, and works the blended polymer to make it a consistency easier for the calendar to handle. The polymer is then sent through the calender and its thickness is dependent on the gap between the last two rollers.”
Though the calendering equipment has improved since the introduction of EPDM, the process does produce inconsistencies in the finished sheets, especially in very thick and very thin gauges. According to the aforementioned article, “If the thickness is below 0.006 inches then there is a tendency for pinholes and voids to appear in the sheets. If the thickness is greater than about 0.06 inches, though, there is a risk of air entrapment in the sheet.”
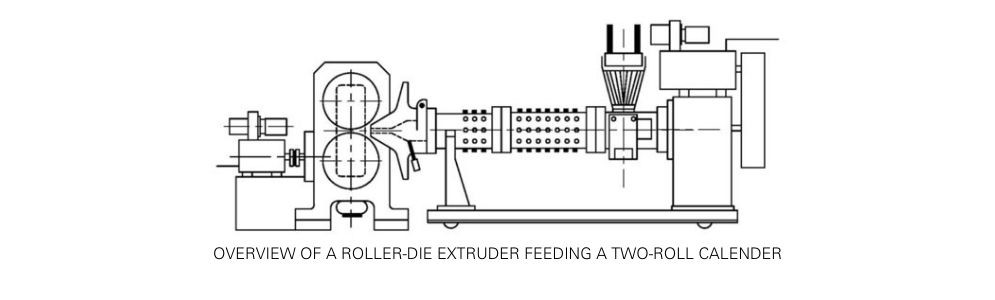
Instead of calendering, Johns Manville EPDM is manufactured by means of extrusion. This technique has been tested and recalibrated many times to ensure the highest standards of membrane quality. There are, indeed, calender rolls on an extrusion line, but they are post-blending. For the purpose of this article, “calender” is used when describing how the polymer and formulation are blended before moving to the sheeting process.
Extrusion: modernizing the process
The process starts with creating the formulation from raw materials. Once the various ingredients are mixed together into uncured rubber, it is ready to be processed into uncured sheets. EPDM is often made by producing two thinner sheets that are cured together to make one; this redundancy creates a higher-quality product. During this process two separate extruders are used.
After mixing, the hoppers at the extruders are loaded with material that can be in the form of either pellets or slab. From there the material enters the feed throat of the extruder and goes through a scraper that removes any material that sticks to the screw or starts to reverse. Inside the screw itself, multiple rows of pins are spaced throughout the extruder. The pins are located in many different positions within the extruder. The pins are used to combine and masticate the material together and can be configured to adjust where the most intense mixing occurs.
From there the process is controlled using TCUs (temperature control units) on the screw in the extruder, as well on the walls along the various zones in the extruder barrel. The TCUs are used to maintain a temperature at which the rubber flows without adding unnecessary heat to the mix. The goal is to blend the material together while avoiding curing the material. In addition, there is a differential temperature between the wall and the screw to aid in the material flow process. The material then passes over a temperature sensor at the end of the extruder that monitors the rubber temperature as it is leaving the screw and entering the die. The die is configured with temperature control on the top and bottom, again to avoid curing, but to maintain flow. At this point in the process, the material is fully blended, and the goal is to use the die to expand the compound in preparation to make a sheet. As the material leaves the die, it goes through a set of lips that sets the shape of the material before the final sheeting (post-blending calender) step of the process. The die lip design influences that particular compound’s flow characteristics. The screw speed can be adjusted to maintain a constant feed rate, which, in turn, creates a more consistent thickness profile and eliminates surging, which is common with traditional calendaring.
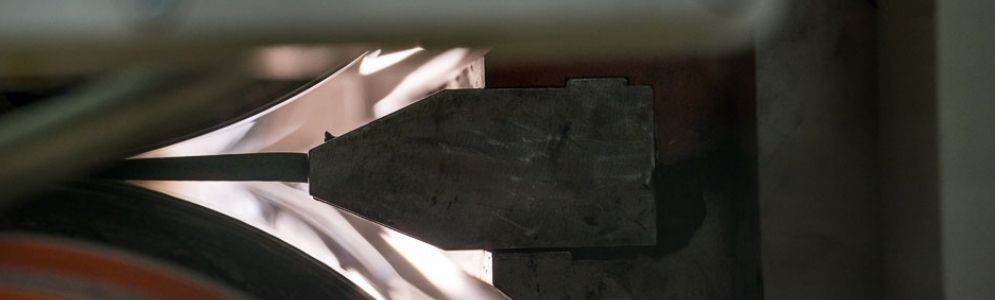
The material leaving the extruder is kept to a 1-to-1 ratio with the adjacent sheeting rolls (calender rolls), which eliminates a rolling material bank. It is simply pushed out through the die in the form required. Traditional calendering requires a large rolling material bank behind the rollers to keep the sheet from having voids or run-outs. The downside of this approach is that it can create a significant number of pock marks or entrapped air. In addition, rolling banks increase unnecessary head cycles to the material, resulting in hot spots and/or scorching. Because the material may not turn over into the nip of the rolls, inconsistencies or cured lumps in the calendered sheet can be caused. Also, a calender is typically fed by one or more mills, which are used to heat up the rubber by working it between two large rollers. The mills also entrap air in the rubber as it is processed. Adding extra temperature cycles and/or overworking the rubber material can cause premature heat aging, which potentially reduces the service life of the finished product. Calendered material also relies on operator involvement in blending the rubber, which introduces other variables as a result of individuals’ varying techniques.
A main advantage of the extrusion process is that it eliminates air gaps (pock marks) in the sheet and minimizes precured lumps. It also allows for better temperature control of the uncured EPDM. The extruder has multiple areas of temperature control: screw, feed throat area, end of screw area, die top and bottom. All of these areas can be heated or cooled as necessary, to minimize scorching of the material, which reduces cured lumps. That is not easily done with traditional warm-up mills.
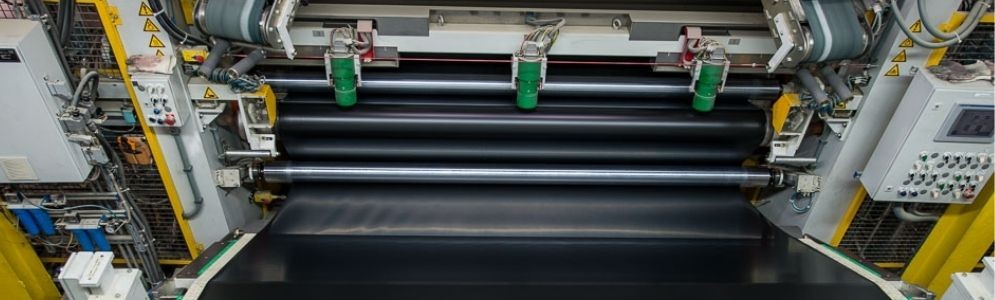
The calender rolls are also fitted with temperature control to cool the rubber quickly and to minimize the rubber sticking to the rollers. The material is trimmed to width after it goes through the calender rolls and is processed through a doubling roll that combines the two half mill sheets. This roller is kept at a fixed temperature and pressure to ensure consistent lamination. Throughout the remainder of the process, the rubber is kept in nearly constant contact with a surface, with the goal of minimizing stretching and deformation. The sheet is monitored via thickness gauges. These gauges blow air on the sheet and monitor the backpressure and distance between the axes of the rollers to calculate the thickness. The sheet is also monitored with a grayscale visual defect system, which takes a reference image every five minutes. If the system detects a difference on the sheet, it will alert the operator. As a result, extrusion delivers tighter uniformity of thickness across the sheet to provide a subtle but critical difference from calendering. This subtle difference provides enhanced seam performance and increased longevity of the membrane.
Extrusion: less labor with higher quality
Since the finished material is more uniform and has little or no surface porosity or air pockets, less backing material or parting agent is needed to keep the sheets on the rolls from sticking together during the vulcanizing process. This means there is less employee time required to prepare the membrane for installation, and the contractor has a much better chance of getting a stronger seam, removing some margin of error. Less time spent preparing the membrane means potentially lower labor costs.
During a time when the building trades–especially roofing–are experiencing a critical shortage of labor, having a membrane that is easier and quicker to install and allowing a crew to do more work in less time is of paramount importance to a contractor’s bottom line.
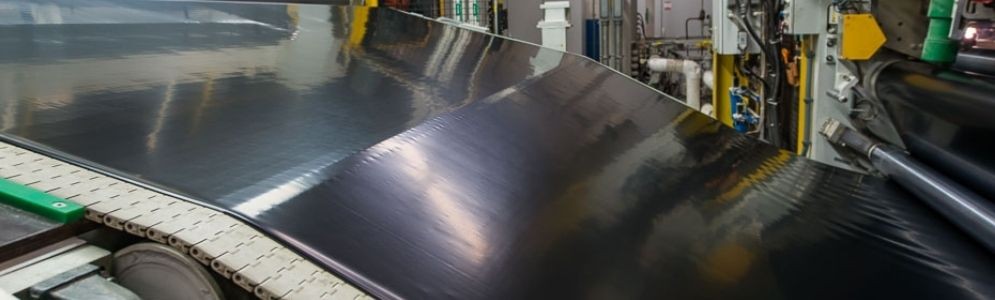
Extrusion: greater consistency for longer life
As previously noted, extruded sheets exhibit a more consistent, smoother surface that is free of pockmarks, voids or entrapped air, yielding full thickness consistently across the sheet. The most common failure modes for an EPDM membrane are seam performance and a loss of mil thickness over time that leads to thin spots or holes.
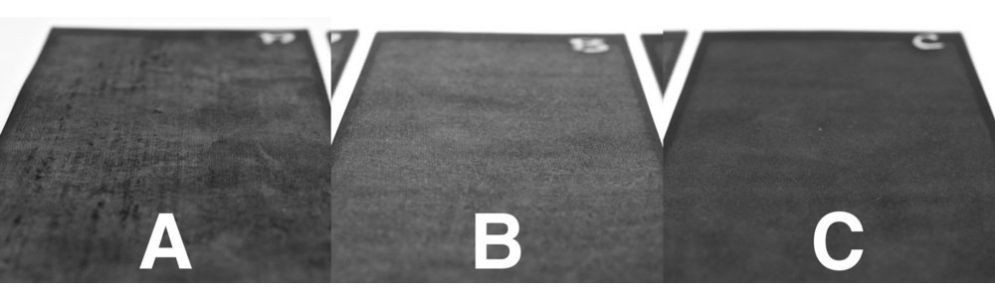
Once exposed to the tough roof-top stresses of an ever-changing environment, any voids or pockmarks where there is a loss in thickness will be the most likely place for a failure to begin. Ultimately, this will result in a leak. By ensuring a consistent thickness across the sheet, an extruded membrane eliminates these potential problems, helping extend the life of the roof system.
Furthermore, the consistent thickness results in a smoother sheet, leading to better lay-flat qualities. This enables easier installation on adhered systems and appearance is enhanced due to lack of wrinkles or “waviness.” In comparing JM’s extruded sheets (option C in the above picture) to more traditional calendered products, the Milan-produced membrane was found to have 40% less thickness variation across the width.
With building owner’s maintenance budgets constantly under pressure, using a membrane with less surface defects on the day of installation can lead to a longer service life and lower lifecycle costs.
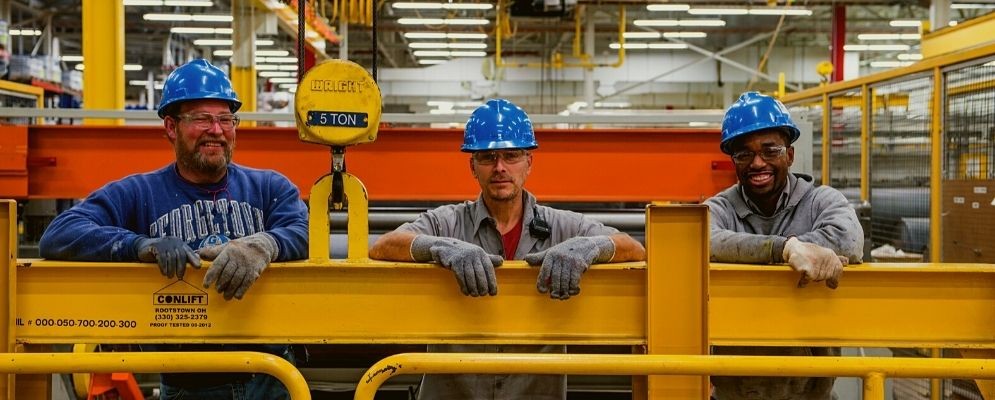