Spiral ducts are very common in today’s commercial settings. They offer a myriad of benefits ranging from longer duct runs to reduced leakage because they have fewer joints. Additionally, many architects and designers prefer the aesthetic appearance of a spiral duct over that of a rectangular duct.
Just like many duct systems, however, spiral ducts often require insulation. There are two primary reasons to insulate a spiral duct:
1. Thermal control
2. Acoustical control
In the case of thermal control, the insulation typically serves two purposes. The first is to maintain the temperature of the air within the ducts. This helps improve efficiencies throughout the air handling system because less energy is required to keep the air heated or cooled as it travels along the duct. The second purpose for insulation is condensation control. In humid climates, condensation will form on any duct that is cooler than the dew point. Condensation can damage the structures surrounding the duct, create mold growth, and/or drip onto the floor and create a hazard for building occupants.
When we consider acoustical control, the reasons for insulation have less to do with efficiencies in the system and more to do with improving the space for building occupants. Studies have shown that most people are more productive when they are working in quiet spaces with a minimal amount of background noise. In an office setting, this can often be hard to achieve not only because most office spaces don’t have private offices for everyone, but also because the duct system often connects individual office spaces. This means that if the system isn’t insulated for acoustical control, cross-talk noise carried through the ducting from vent-to-vent, or fan noise, can travel through the ducts, creating louder office environments. For this reason, many building certifications, like LEED, or standards, like ANSI, contain specific noise control requirements for the benefit of building occupants.
There are two types of spiral duct systems: single-wall and double-wall. The double-wall system is an insulated (and sometimes perforated) duct within a duct. The single-wall system is simply a single, metal duct.
Single-wall systems can be lined or wrapped depending on the designer’s purpose for insulating the duct. If the system needs to offer both thermal and acoustical control, the designer should specify a duct liner. Duct liner goes inside the duct, facing the airstream surface. It helps control unwanted fan noise and cross talk in addition to supporting energy efficiency in the system.
Unlike rectangular ducts, lining spiral ducts requires a material that can conform to a curved inner surface rather than a flat surface. Because of this, pre-kerfed duct liners, like Spiracoustic Plus®, are often the easiest method for lining spiral ducts.
The kerfs (grooves) cut into Spiracoustic Plus are spaced to fit the specific duct diameters ranging from LD (large diameter) to our newly released VVSD (very very small diameter) ducts*.
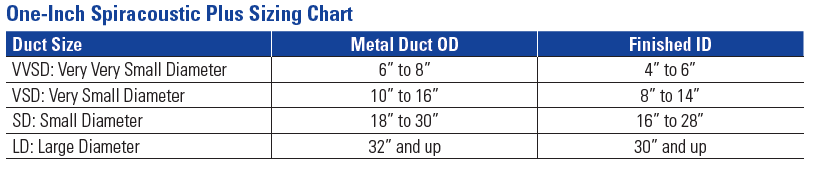
*In one inch only
The one-inch VVSD Spiracoustic Plus from Johns Manville is the only pre-kerfed duct liner designed specifically to fit in ducts with diameters between 6 and 8 inches. This allows contractors to ensure that the Spiracoustic Plus fits exactly into the duct size they are insulating and helps improve the installation process and quality in these smaller duct sizes.
Beyond offering a snug, custom fit for a complete range of duct sizes, Spiracoustic Plus comes with an airstream surface that is factory-coated with Permacote®. This coating is designed to help protect the fiberglass substrate from damage and helps ensure a smooth, robust airstream surface. Lining single-wall systems on straight runs is also a relatively simple process. Detailed video instructions for insulating straight runs and fittings with Spiracoustic Plus can be found here.
Duct liner isn’t the only solution for spiral ducts, however. If system designers aren’t concerned about acoustics, and are strictly worried about thermal control and moisture prevention, wrapping the ducts in duct wrap like Microlite® is often the best solution. Microlite comes with three different facing options: foil scrim kraft (FSK), white poly scrim kraft (PSK), and black poly scrim kraft (PSK). Each of these facing types has a perm rating of <0.02 to help prevent moisture drive and condensation.
If the duct system will remain exposed, system designers can choose the white or black PSK facing for aesthetics. It is important to keep in mind, however, that duct wrap does not offer acoustical control.
Double-wall systems require entirely different insulation because they are structured differently with an insulated inner duct and an outer duct that encases the insulated inner duct. Typically, these systems are insulated with a flexible, blanket-type insulation like Spiral SG. This insulation is wrapped around the exterior of the inner duct, which is then inserted into the outer duct. This system offers both thermal and acoustical control, however, it is typically heavier and can be more expensive than a single-wall system because it requires the use of substantially more metal.
As HVAC system designers consider their options for spiral duct systems, understanding the benefits and drawbacks of single versus double-wall systems as well as the strengths and weaknesses of the insulation materials available can help them create a high performing HVAC system that meets their needs.
To learn more about insulating ducts for acoustical control, please register for our upcoming Insulation Intel® webinar, Optimizing Acoustical Control in HVAC Systems.