As the world shifts toward cleaner energy and electrification, storing energy reliably is more important than ever. From cars and trucks to forklifts, data centers, and solar backup systems, batteries play a critical role in keeping our lives powered. And while newer technologies often capture the headlines, there’s another battery type quietly powering the backbone of modern life: the lead-acid battery. Reliable, cost-effective, and highly recyclable, lead-acid batteries are still a go-to choice for many automotive and industrial applications. And the best part? These batteries are getting better. Smarter materials and designs are making them more powerful, durable, and efficient. That’s where we come in.
At Johns Manville, we provide advanced materials, including polyester and glass nonwovens, glass microfibers, and glass sliver, that help lead-acid batteries perform at their best. Whether it’s improving battery life, reducing manufacturing issues, or boosting reliability in tough conditions, our materials make a difference. Here’s how.
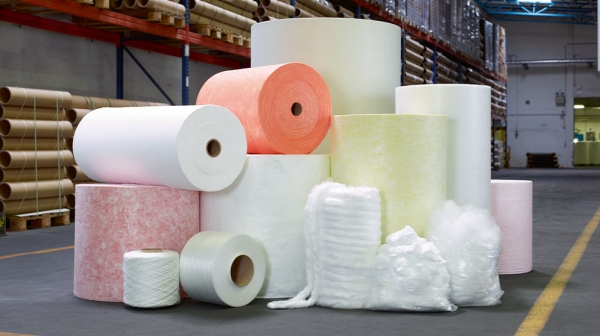
Back to Basics: What Is a Lead-Acid Battery?
Let’s take a quick step back. A battery is essentially a chemical storage tank for energy. When you use it, chemical reactions convert stored energy into electricity. Batteries rely on the interaction of four core elements: hydrogen, oxygen, lead, and sulfur.
Lead-acid batteries come in several types:
- SLI (Starting, Lighting, Ignition): These are the classic car batteries. They deliver short bursts of power to start engines and run electronics. Not designed for deep discharge.
- EFB (Enhanced Flooded Battery): A more robust version of SLI batteries, designed for vehicles with basic start-stop technology. Offers improved charge acceptance and cycle life.
- AGM (Absorbed Glass Mat): A sealed, maintenance-free battery used in high-performance vehicles with advanced start-stop systems and features like regenerative braking. Handles deep discharges and rapid recharging well.
- Deep Cycle: Designed to deliver a steady amount of power over a longer period. Commonly used in forklift trucks, golf carts, marine applications, and renewable energy storage systems.
All of these have different needs, but they all rely on smart, well-engineered materials to perform reliably.
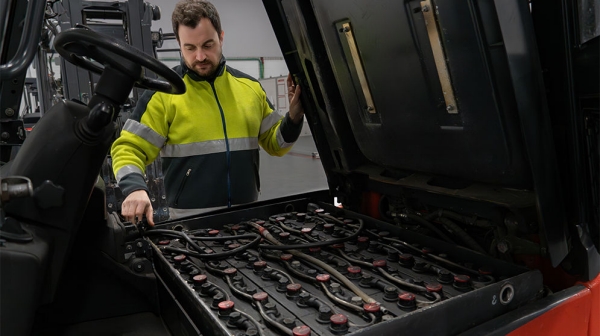
Pain Points in the Battery World and How We Help
Let’s talk about the challenges battery makers face and where our products step in to help.
1. Paste Bleed-Through
❌ The problem: During the battery plate pasting process, soft lead paste can “bleed through” the separator or carrier layer, leading to contamination, poor adhesion, and even short circuits.
💡 Our solution: JM’s high-performance glass fiber pasting papers act like a shield and a sponge at the same time. They hold the paste in place within the grid structure, minimize material loss, and improve bonding with the lead grid. This results in cleaner equipment, improved process control, and longer-lasting battery plates.
2. Tearing on Production Lines
❌ The problem: On high-speed production lines, material strength matters. Weak or uneven carriers can tear, leading to production slowdowns and costly downtime.
💡 Our solution: JM’s products are engineered for high tensile strength and dimensional stability, which keeps production lines running smoothly. Less tearing = fewer headaches.

3. Inconsistent Battery Performance
❌ The problem: Poor encapsulation or plate integrity can lead to reduced performance, shorter battery life, or increased return rates - especially in demanding applications like EFB or AGM.
💡 Our solution: JM helps stabilize the active material and promote consistent charging and discharging cycles. In AGM batteries, the nonwovens mat absorbs electrolytes while acting as a stable medium that maintains plate separation and supports ionic flow. This results in higher power density, longer battery life, and improved safety.
4. Pressure to Cut Costs Without Cutting Corners
❌ The problem: Everyone wants better performance, but no one wants to pay more. Battery manufacturers need materials that help them reduce long-term costs by improving efficiency, durability, and process reliability.
💡 Our solution: JM’s polyester and glass fiber products for battery applications are engineered for long-term value. While they’re premium in quality, they help to reduce waste, cut downtime, and extend product life. That’s how we help lower total costs across the full battery lifecycle, not just the bill of materials.
Why JM Is a Partner, Not Just a Supplier
In the U.S., we work closely with converters and battery manufacturers to deliver materials that meet real-world production challenges. Our advantage is in our ability to customize solutions, respond quickly, and back it up with solid technical support.
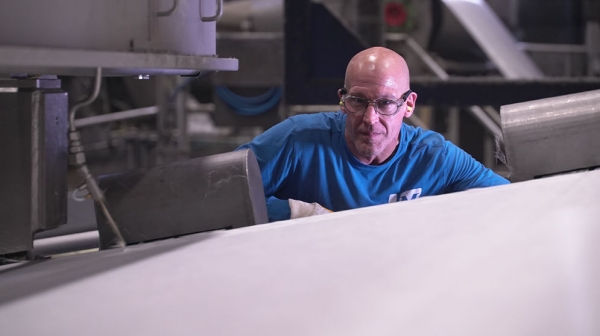
✔️ Full range of high-quality solutions: From PET nonwoven for gauntlets and separators to a full range of glass materials ranging from microfiber to sliver and glass nonwovens
✔️ Domestic supply chain that avoids long delays or import hassles
✔️ Strong adhesion and chemical resistance
✔️ Deep battery knowledge and R&D support
✔️ Reliable partner with responsive customer service
Let’s Build Better Batteries Together
Whether you make SLI, EFB, AGM, or deep cycle batteries, chances are you're looking for ways to improve quality, reduce line issues, and meet customer expectations. JM materials can help you get there.
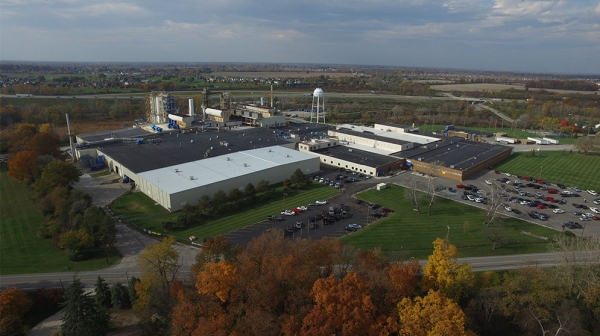
Want to learn more? Let’s talk.
Our team is here to support you with smart materials, deep expertise, and great customer service.
-
Engineered ProductsWhat Keeps Energy Flowing: The Unsung Role of Materials in Lead-Acid Battery Performance
-
Engineered ProductsWhy Exterior Sheathing Needs a Tough Partner – And Why Our Fiberglass Nonwovens Are Up for the Job
-
Engineered Products
-
Engineered Products
-
Engineered Products
-
Engineered Products
-
Engineered ProductsHow to Solve Industrial Filtration Challenges with Evalith® Micro Fiberglass Filter Tube Media